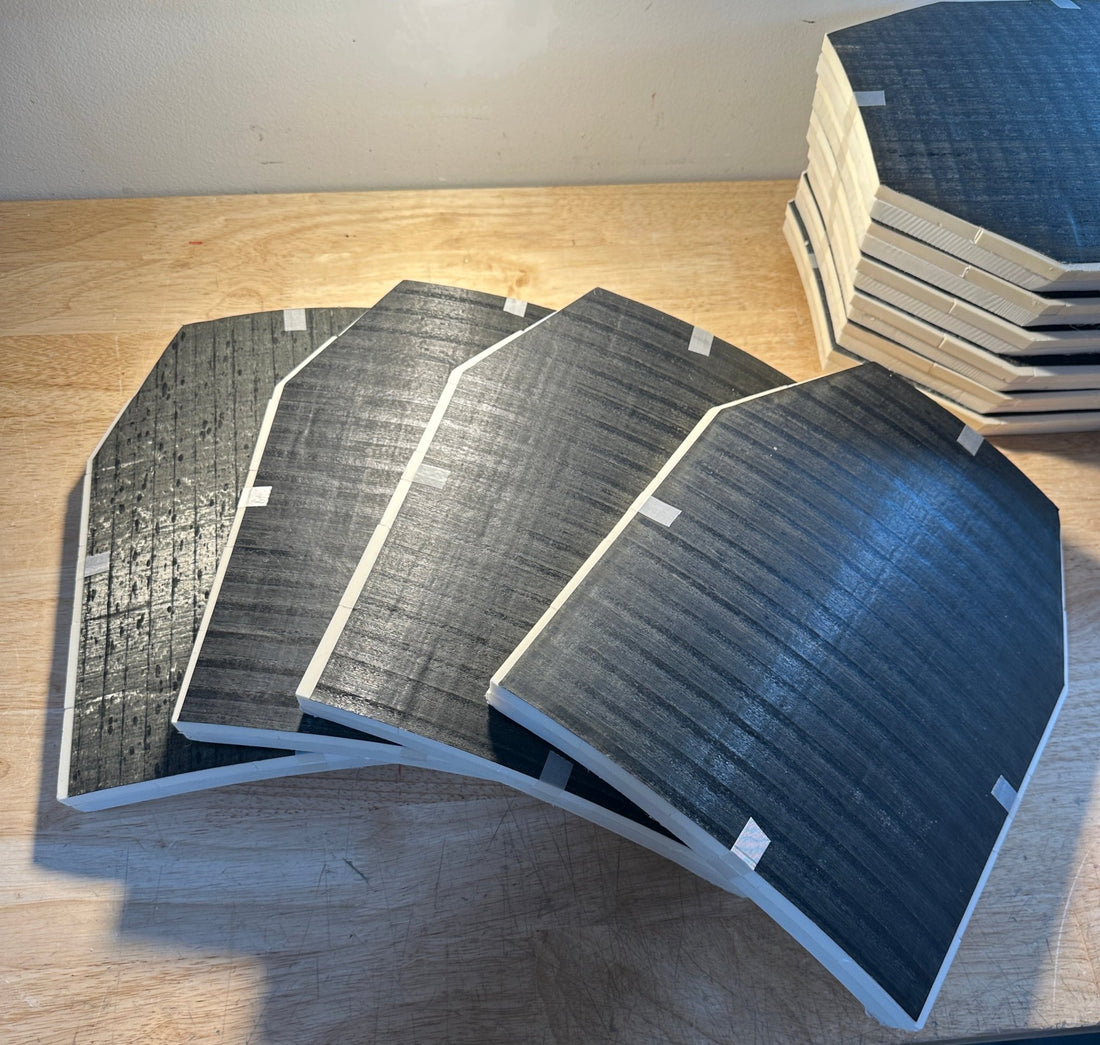
Composite strike face covers and crack arresting layers on ceramic armor
It still surprises me that well-known ceramic armor manufacturers continue to neglect the addition of crack arresting technology to their armor plates. This issue is not discussed often, but the performance implications are so significant that I wanted to touch base on the issue here.
Monolithic ceramic armor plates are by far - what most well-known companies use as a strike face material. Monolithic plates are utilized due to the lack of available small sizes in the USA, ease of armor assembly and autoclaving methodology. Monolithic plates are single pieces of ceramic. These one-piece tiles are vulnerable to across plate cracking when shot. They usually fracture when shot, creating cracks in the armor that act as weak spots. For the plate to withstand additional projectiles in this condition, there must be a way to secure these fractured elements, preventing their motion relative to one another as the wearer is active and/or when other rounds arrive. Alumina ceramic is more dense and less brittle than silicon carbide - but all ceramic material in monolithic designs are prone to cross plate ballistic energy transfer and damage that ripples along the adhesive layering in an attempt to escape the armor.
For both mosaic and monolithic designs - advanced ceramic build techniques will incorporate a "crack arresting layer" that protects the strike face from ballistic energy moving through armor. This crack arresting layer holds newly fragmented ceramic together. But, it serves another purpose... it reduces the size of the spall radius found on the reverse side of the strike face.
The spall radius is an area on the reverse side of the strike face that fractures away in a circular design, thinning the ceramic material. The plate is highly vulnerable to additional rounds (even of lower calibers than the original) within this thinned out area. Shots within 2.5" - 3" of the original projectile have elevated probabilites of passing through the armor because of the spall radius and proximity of the thinned ceramic strike face.
The image below shows an alumina monolithic plate on left and an alumina mosaic plate on right with crack arresting technology. The back side of the strike face is shown, where the ceramic meets the polyethylene backer. The monolithic was shot one time with .30 M2AP. The mosaic was shot twice with .30 M2AP. The increase in effectiveness of the mosaic style and crack arrestors is clearly seen in images and in the data over a number of years of our testing.
Many of our videos on social media have addressed the subject of spall circles on monolothic plates. To be successful in resisting multiple projectiles over the longer term - crack arresting technology must be deployed in ceramic armor. The crack arrestors can be aramid, polyethylene - or a combination of both. They can also be made out of non-ballistically resistant materials. There is great benefit to crack arrestors in the 2-4mm thickness range as they reduce the amount of ceramic "dust" ejecting from the strike face when struck.
Some social media "experts" claim that aramids are rarely used in armor any longer. For experienced builders, this simply is not the case. Aramid can be pressed 45/90 degrees along with other materials like carbon fiber or Vectran® fiber. Some materials combinations can be stiffened up and used as trauma reducers... while a different percentage combinatio of the same materials could be used as a crack arresting layer on the armor strike face.
One challenge in using crack arresting layers is to develop (or discover) the most effective adhesive that can function well on various types of ceramic and act as a suitable bed for finishing materials. One side will meet a ceramic material (aluminum oxide, silicon carbide or boron carbide) and the other will meet the rubber or nylon cover. In most cases, adhesives that will bond to alumina may not bond well to silicon carbide... or a silicon carbide, boron carbide hybrid. So - adhesives are an important challenge.
Through the years, we have developed a one adhesve solution deployed throughout the armor system. That was a challenge - but also a boon to performance for us. If there is one thing that makes or breaks armor systems - it's the adhesives.
Many well-known manufacturers carefully control what you see on social media and are hesitant to share test reports for products over the long term. Many have test reports that have not been updated in years.
Monolithic plates can be effective - but they must be built properly to get the highest amount of available performance.
We strive to use the latest technology so that you get the most performance per dollar spent. We are transparent with our testing reports. At our price point, we will go up against any other supplier - any time.